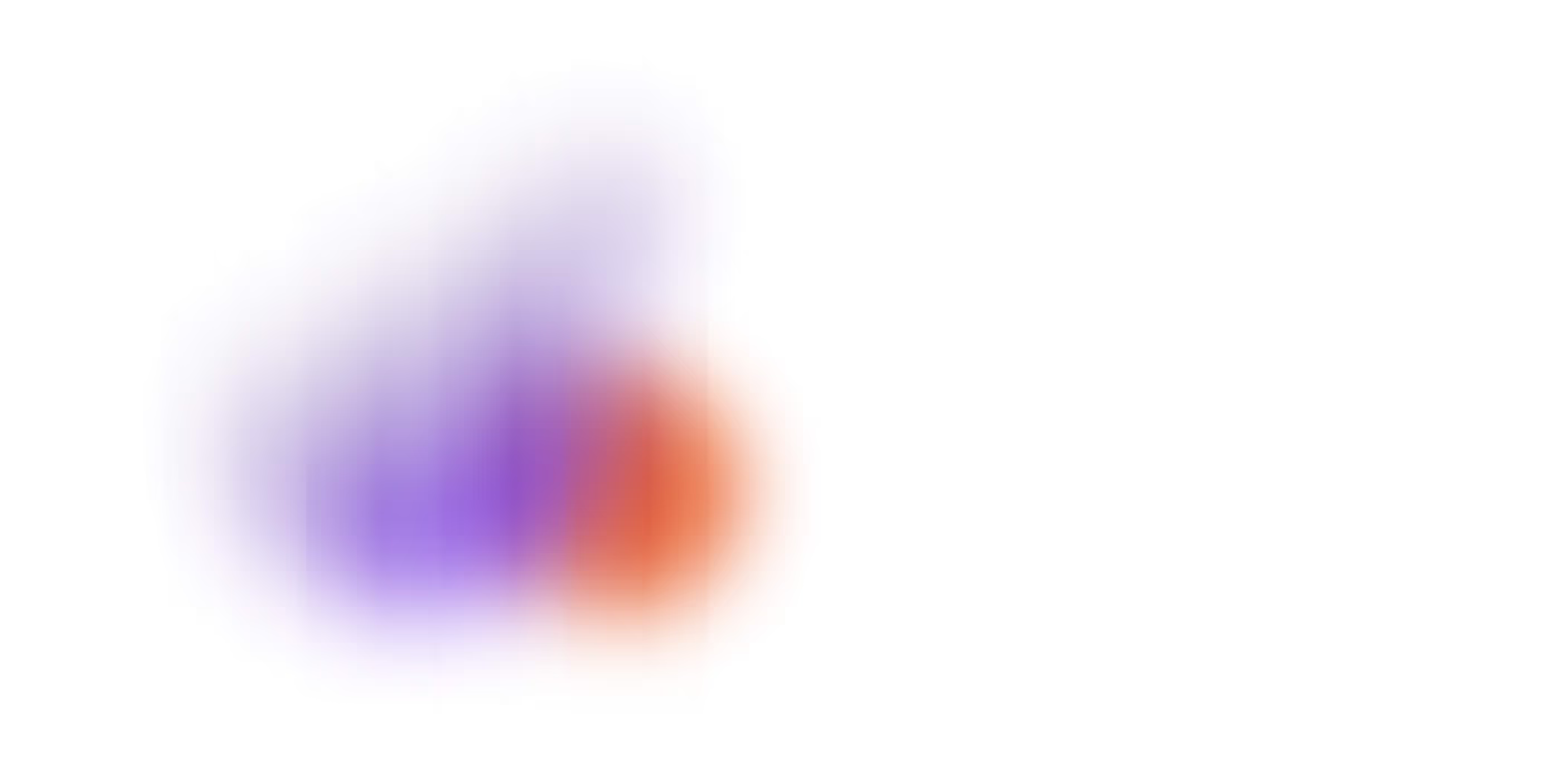
Supply Chain
The Hidden Costs of Inefficient Supply Chain Operations: What Retail Leaders Need to Know
Hidden costs and back-end inefficiencies can quietly drain profits and stall growth from retail businesses. Discover how to fix it with Lyzer.
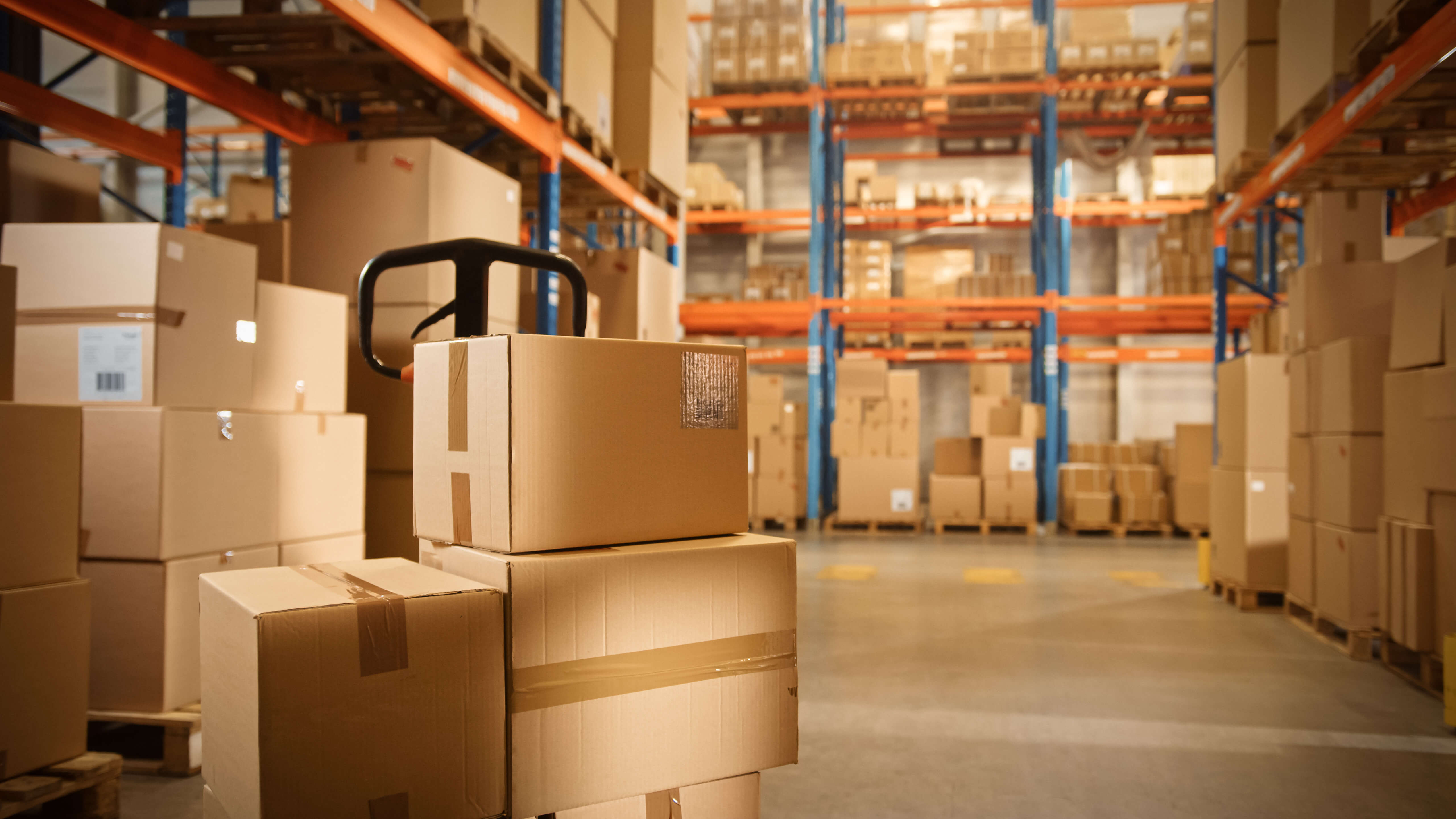
Uncovering the Hidden Costs of Supply Chain Inefficiencies
Let’s be honest: in retail, the supply chain can make or break your business. Everyone talks about optimizing inventory or speeding up delivery. But what often flies under the radar is how day-to-day logistics — order management, fulfillment, and last-mile delivery — can quietly drain your profits if they’re not running smoothly.
At Lyzer, we collaborate with fast-growing retailers every day. And we’ve seen how small inefficiencies in operational execution can snowball into late deliveries, unnecessary costs, and lost customers. It’s not just a tech issue — it’s a growth killer.
Here’s what every retail leader should know about the hidden costs of inefficient supply chain operations — and what you can do to eliminate them.
What Do We Really Mean by Supply Chain Inefficiencies?
More than compliance frameworks or financial audits, Lyzer focuses on the day-to-day execution that actually keeps your retail operations moving. Think about the real engine behind every successful order:
- Orders coming in are processed instantly.
- Items picked, packed, and ready to go.
- Clear, real-time tracking across every step
- Deliveries happen without delays or confusion.
- Systems talking to each other without manual fixes.
- Repetitive tasks automated so your team can focus on higher value work.
Where Inefficiencies Hurt the Most
Let’s look at the specific areas where operations tend to break down: the points in your logistics flow where small issues quietly grow into bigger problems if left unchecked.
1. Manual Processes = Expensive Mistakes
When teams rely on spreadsheets and manual data entry, the chance for error goes way up. An error or missed order can delay shipments, frustrate customers, and create a mess that takes hours to untangle.
2. Disconnected Tools
If your fulfillment software doesn’t talk to your delivery platform or customer systems, you’re wasting time reconciling data manually. That kills agility and slows down your response to problems.
3. Delays That Cost Sales
Customers expect fast, seamless delivery. If orders get delayed due to clunky back-end processes, they’ll go elsewhere next time — and your brand pays the price.
4. Limited Visibility
Without real-time data, you’re guessing. That makes it hard to spot bottlenecks, adjust resources, or act on issues before they escalate.
5. Wasted Time on Repetitive Tasks
Approving orders, updating records, sending status emails — your team shouldn’t be doing all this manually. It’s not just inefficient; it’s draining.
What Causes the Bottlenecks?
So, what’s behind all these slowdowns? In our experience, it usually comes down to outdated workflows and legacy tech that simply weren’t built for the speed and complexity of modern retail.
For starters, many retailers are still using systems that don’t integrate with each other. You’ve got your order management in one place, warehouse software in another, and delivery tracking somewhere else — and none of it talks. That means someone on your team is stuck manually syncing data, which slows everything down and opens the door for mistakes.
Believe it or not, paper-based processes are still surprisingly common. Whether it’s printed pick lists or handwritten delivery notes, these old-school methods are not only inefficient — they’re hard to track, easy to lose, and impossible to scale.
Communication is another big one. When your team is juggling emails, spreadsheets, and phone calls just to stay aligned, critical information slips through the cracks. And that leads to confusion, delays, and missed expectations.
Finally, there's the automation gap. Too many businesses still rely on manual steps for tasks that could easily be automated — like order confirmations, status updates, or delivery notifications. This creates unnecessary work, reduces agility, and burns out your team.
The result? When your back-end logistics aren’t flowing efficiently, the downstream effects hit your customers — with late deliveries, order errors, and poor experiences that are tough to recover from.
How Lyzer Helps
We built Lyzer to solve these exact challenges by focusing on where it counts: operational logistics.
Here’s what we bring to the table:
Streamlined System Integrations
We connect the systems you already use — from order management to logistics platforms — so your data moves automatically and in real time.
Automated Order Fulfillment
From order to doorstep, we simplify each step to reduce errors and speed things up. Your customers get what they want faster.
Visibility and Tracking
Know where everything is at every moment. Get alerts, see bottlenecks early, and fix them before they hit your bottom line.
Automation Where It Matters
We automate key logistics workflows — confirmations, updates, internal alerts — so your team isn’t stuck doing repetitive admin.
Lyzer helps your company to move things from A to B with maximum efficiency.
The Payoff: Smarter Operations, Better Margins
When your operations are firing on all cylinders, everything just works better.
Orders get out the door faster. Deliveries land where and when they should. Your team stops wasting time on manual tasks and starts focusing on what really moves the needle. Customers notice the difference — and they come back for more.
And the best part? While you’re delivering a better experience, your costs go down and your margins go up.
That’s the kind of win-win we’re here to build.
Ready to Clean Up the hidden costs of inefficient supply chain operations?
Don’t let back-end logistics hold your business back.
Contact Lyzer to learn how our logistics-focused solutions can help you streamline operational processes, reduce costs, and stay ahead of the competition.
Sources:
Discover the right solution for your challenges
Contact Lyzer to learn more about our innovative logistics solutions.